Rewinding Line
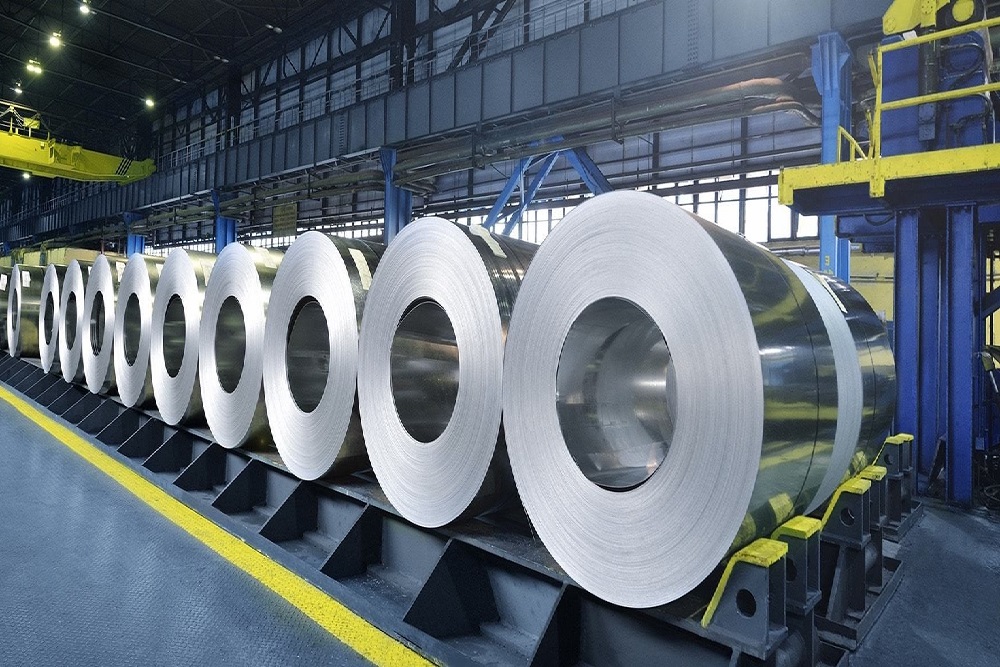
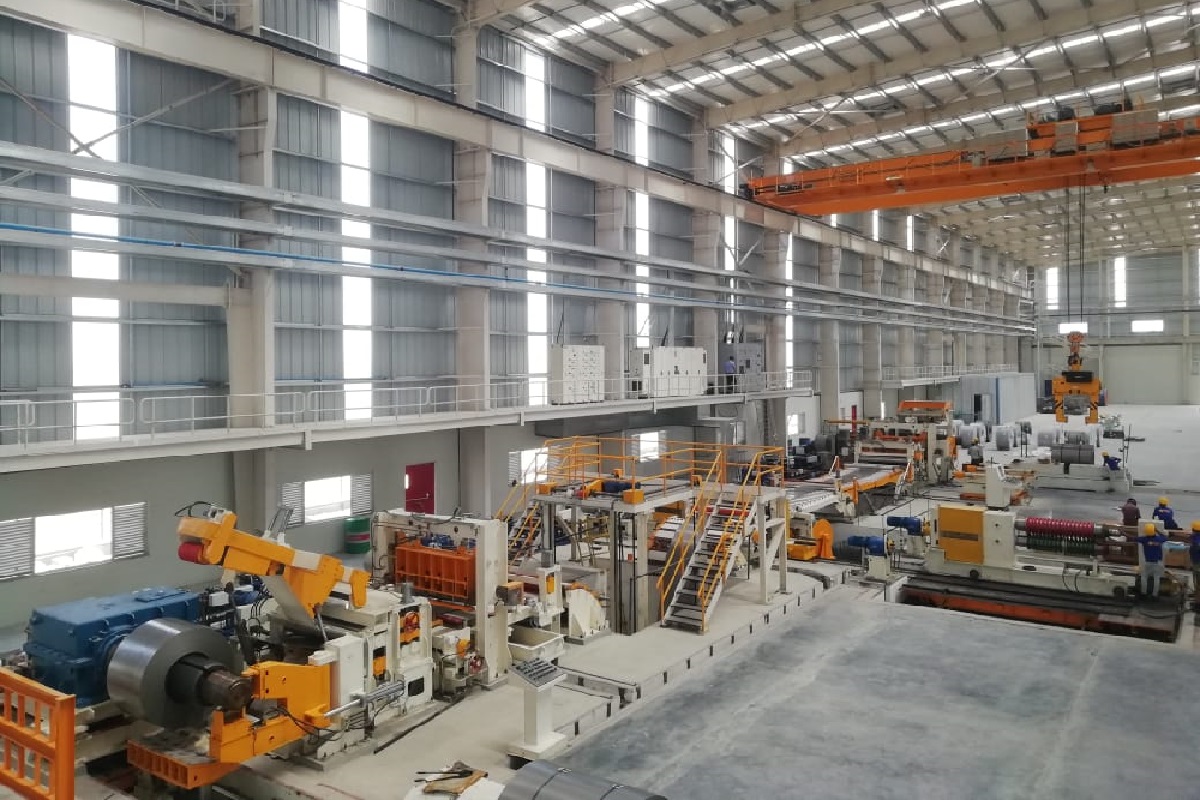

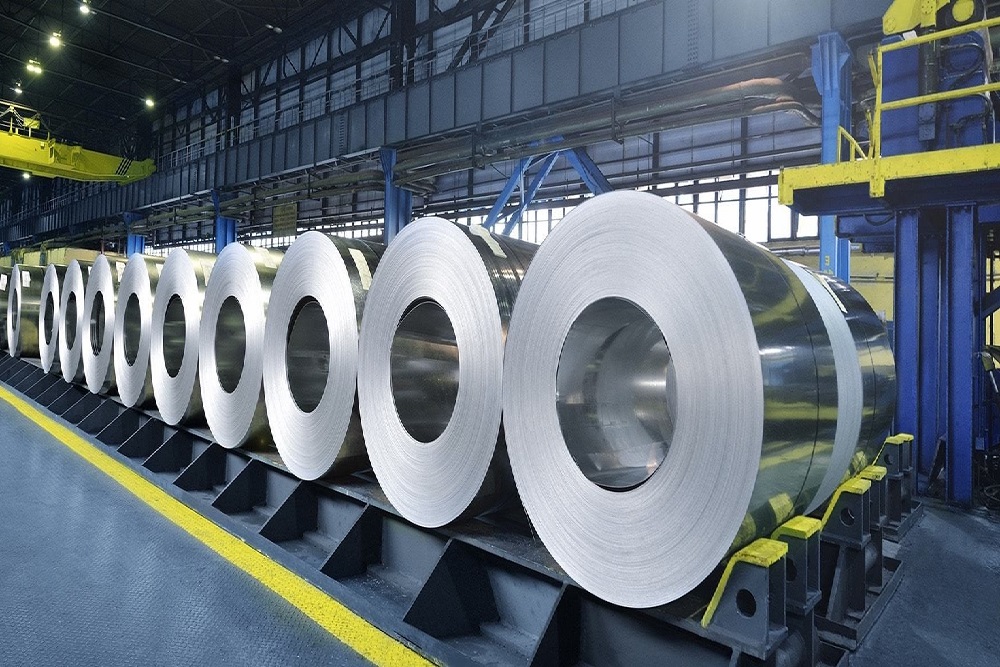
We use center position control (CPC) at the pay off and edge position control (EPC) at the recoiler for maintaining the perfect coil edge. Depending upon the overall layout, we provide different designs of outboard bearing supports at uncoiler and recoiler. For rewinding of thinner gauges, we provide Belt Wrapper at the recoiler.
We supply rewinding cum trimming lines for a thickness range of 0.15 mm to 3.2 mm, maximum width of 2000 mm and max speed of 700 MPM. We use two-speed gear boxes to trim and rewind thicker gauge coils at lower speed. This helps in optimizing the motor power and energy saving.
Load cell is provided in the exit coil car saddle to weigh the finished coil.
Hot rolled steel coils are coiled at high tensions during the process of rolling. The steel is work hardened and is annealed in batch annealing process in Bell Furnaces under inert atmosphere of Hydrogen. The steel coils are rewound under lower tension and stacked in Bell Furnaces or else the wraps of coils would stick at high temperature annealing process.
Also many customers demand full hard coils with trimmed and uniform edges and a uniform width. Trimmer heads are precision equipment and need a precise gap control between the blades for burr free trimming. We provide single motor driven trimmer heads which have a precise eccentric gap control. The heads can be driven or non- driven depending upon the operator selection. Mostly we use back tension to provide the necessary tension at coiling by running pay off reels in regenerative mode.