Galvanizing & Galvalume Lines
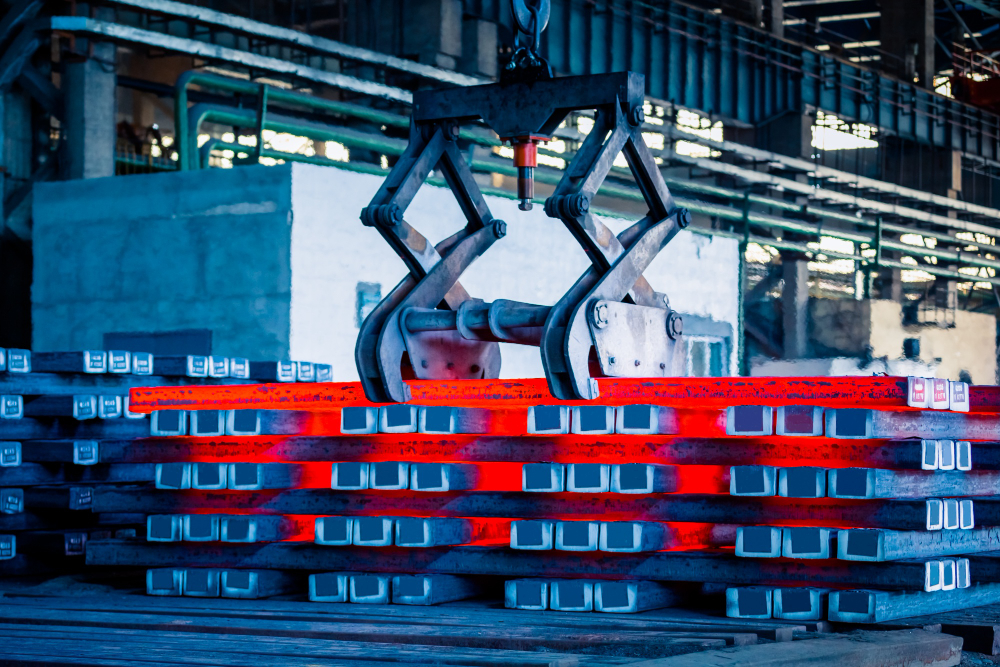
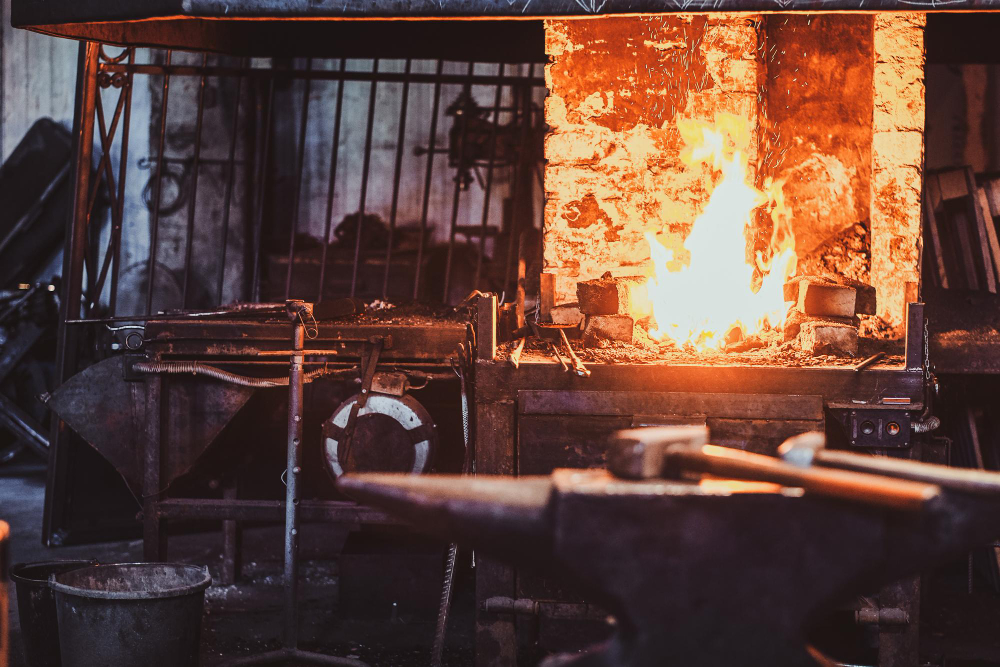

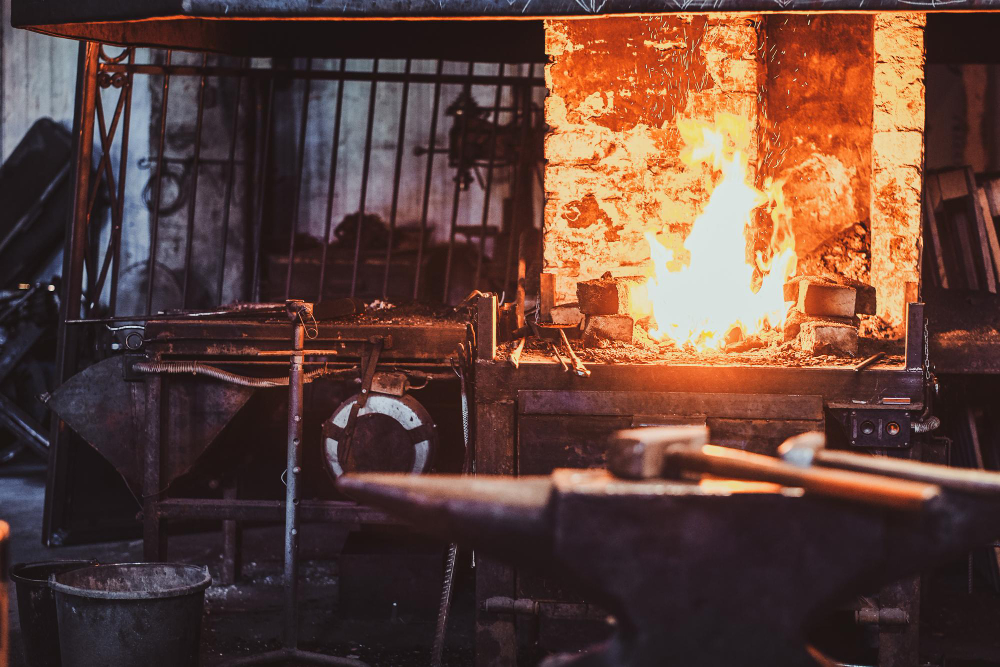
Hot Dip Galvanizing & Galvalume Lines
We supply hot dip Galvanizing & Galvalume Lines in different proportions of Zinc and Aluminium, and color-coating steel lines covering a wide range of coating thicknesses. Depending upon the steel grade and thickness and production capacity, our lines are designed for different speeds with a maximum speed being 180 MPM and a width of up to 2000 mm. Coating thicknesses vary from 40 GSM to 350 GSM. Each line is equipped with a high-quality annealing furnace compatible with a wide variety of steel grades. The stability at high speeds is ensured by optimizing roll design, steering system and precision tension control.
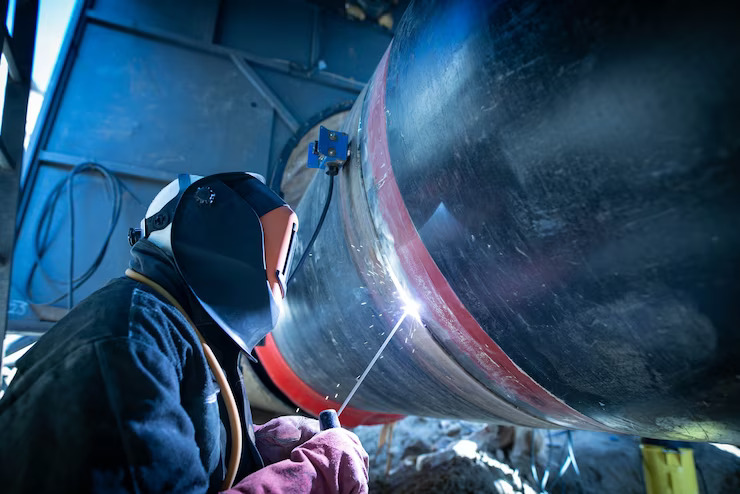