Skin Pass Mill
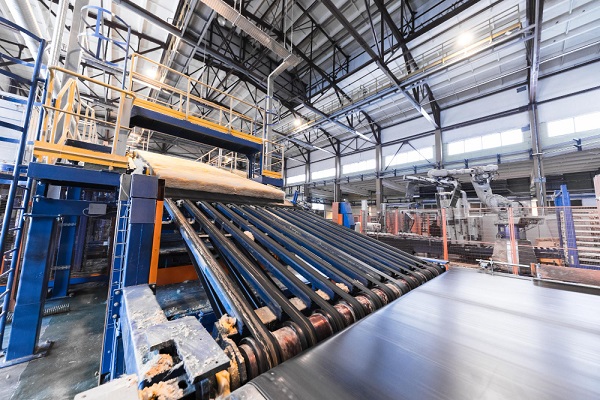
6 HI Reversible Cold Rolling Mill x Max 1550mm Wide x 35ton x Max 1400mpm
Total No of Line Supplied: -
4 Hi & 6 HI Reversible Cold Rolling Mills – 35 Nos
2 Hi & 4 Hi Skin Pass Mill – 20 Nos
Over 30 years of experience in the design and production of rolling mills. Its latest-generation cold rolling mills are designed to be extremely efficient and flexible and to consistently meet the specific needs of its customers, reducing downtime, monitoring tension and tracking and ensuring optimal product thickness and evenness. This value is even further enhanced thanks to tried and tested equipment such as shearing systems, tension levelling, descaling facilities, mandrels, and winders, all of which play a key role in the modernization and installation of new rolling mills and tandem cold mills.