Why Multistage Centrifugal Pumps Are the Ideal Choice for High-Pressure Descaling in Steel Mills
In the hot rolling of steel, surface quality directly impacts final product performance. A critical process in achieving smooth, defect-free steel is descaling—the removal of mill scale formed on the surface during reheating. To carry out this task effectively, the pumping system behind the high-pressure water jets must be both robust and reliable. Multistage centrifugal pumps offer a proven advantage in this demanding application, and here’s why.
Understanding Descaling in Steel Rolling Mills
Descaling involves directing high-pressure water jets onto hot steel slabs to dislodge and remove the oxide layer (mill scale) formed during reheating. This process is essential to prevent surface inclusions, extend roll life, and ensure a clean base for further rolling. A well-executed descaling operation improves not only visual quality but also structural integrity.
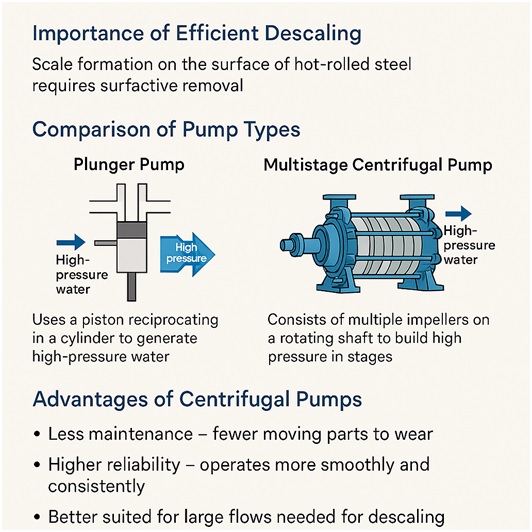
Plunger Pumps: High Pressure, Limited Flow
Triplex plunger pumps are designed to deliver high-pressure water using a reciprocating piston mechanism. They perform well at pressures above 350 bar and at flow rates up to about 60 m³/h. However, their efficiency declines over time due to seal and valve wear—especially when the pumped water contains mill scale and suspended solids. These pumps require frequent maintenance and are generally unsuitable for large flow requirements, which are common in steel descaling applications.
Multistage Centrifugal Pumps: Built for Volume and Stability
Multistage centrifugal pumps operate by passing water through multiple impellers, each increasing the pressure progressively. These pumps can comfortably deliver 100–700 m³/h at pressures up to 400 bar, making them ideal for large-scale descaling systems. Their flow is smooth and continuous, reducing pulsation stress on the piping and nozzles.
Designed for Fluctuating Duty Cycles
In typical descaling operations, the water demand fluctuates sharply. During a single 2–4 minute slab rolling cycle, the descaling valves open and close 4–5 times, causing sudden spikes in water flow. Prismet Inc.’s multistage centrifugal pumps are engineered with precision balancing drums to absorb axial thrust, and robust shaft and bearing assemblies that withstand these dynamic loads. Flexible plate-disc couplings—offered as standard—are zero-backlash, require no lubrication, and prevent misalignment and vibration transmission to the rotating assembly. These features ensure smooth operation under pulsating service conditions.
Proven Field Performance
Our pumps have demonstrated unmatched reliability across steel plants in the United States, India, and Indonesia. Several units have been operating continuously for over 15 years, with minimal downtime and no major overhauls—testament to our engineering and build quality.
Managing Water Quality for Extended Life
Descaling systems often recycle water, introducing abrasive mill scale and solids into the system. Prismet pumps are designed to handle water with up to 0.1% solids, using wear-resistant materials and internal flow paths optimized to minimize erosion. This gives our pumps a performance edge over triplex plunger pumps, which are highly sensitive to contaminants and suffer reduced volumetric efficiency with time.
Conclusion
For demanding descaling systems in hot steel rolling mills, multistage centrifugal pumps offer clear advantages in performance, durability, and cost-efficiency. Their ability to handle fluctuating loads, tolerate recycled water, and maintain stable output with minimal maintenance makes them the pump of choice for modern steelmakers.
Share Post